To obtain the right data from industrial robots, an effective communication setup is required. We studied the efficiency of different communication options through our testing of the industrial robot Fanuc LR-Mate 200iD with the R30iBPlus Mate controller.
What are the communication options for Fanuc robots?
Nowadays, when Industry 4.0, and an increase in use of robots associated with it, is mentioned in many articles (see ATP Journal 2/2020 or 3/2020 ) it is increasingly important not only to be able to deploy robots, but also to monitor and diagnose their operation.
Robots are sophisticated devices generating large amount of information that can be used for diagnostics - such as information about the condition of drives and joints, the maintenance of components, and more.
The tested equipment
One of our OEM partners recently asked us to examine the possibilities of communication with robots, which are deployed at many of his customers in Slovakia. With the growing number of deployments there also increases of important of good diagnostics. Why? Good diagnostics can save solving the service incidents at the customers (i.e., both time and money). In many cases, the solution of reported malfunctions of robots was done in such a way that a serviceman cleaned the dirty sensor on the robot and it could continue working…
Our OEM partner lent us Fanuc LR-Mate 200iD industrial robot with R30iBPlus Mate controller for testing. It is a robotic arm weighing about 27 kg that is used to work in a protected environment (in a cage), as it can move at a speed of up to 4 m/s and has considerable force.
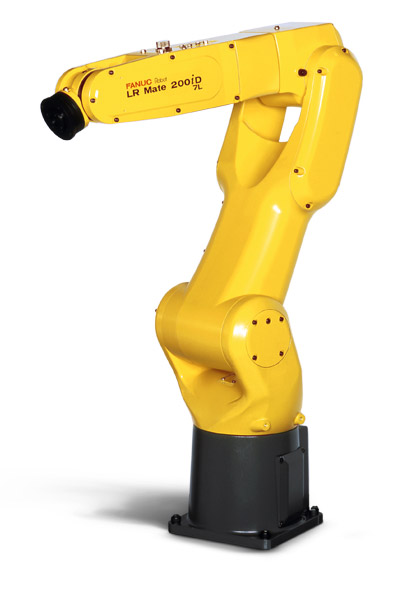
R30iBPlus Mate Cabinet is used to control the robot and communication with the surrounding. For an ordinary person it seems as a quite large metal cabinet (dimensions about 50x50x60 cm) which contains a control unit or other communication cards and input/output cards. This cabinet is connected to the robot by two massive cable harnesses. It also contains three Ethernet ports - two of them are intended for a general use, the third one is reserved for connecting a digital camera.
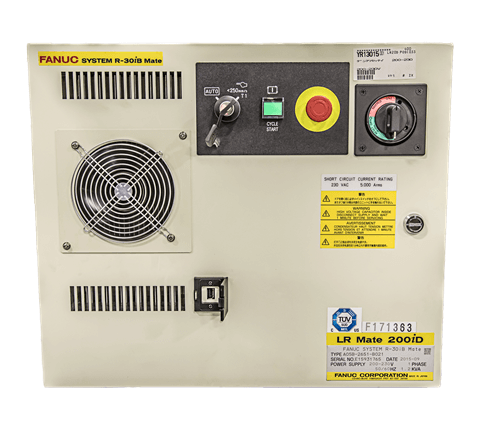
So-called Teach Pendant is used for controlling, configuring and programming this robot. We had borrowed the version iPendant touch, an industrial “tablet” with a touch screen and buttons, which is connected to the control unit with a cable. It contains, for example, “deadman's switch” – the buttons placed on the back that automatically stop the robot if the operator releases or presses the button too hard (e.g. due to a spasm).
In the figure 3 you can also see the red emergency stop button (it should be activated always after the Pendant falls on the ground, but we did not made such tests).
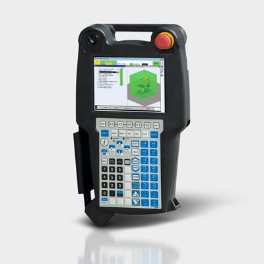
Different Fanuc communication options
What communication options does this robot or its control unit enable? According to information obtained from Fanuc Slovakia, these are following:
· Modbus TCP communication protocol– through the existing Ethernet port, SW license is required,
· Ethernet/IP communication protocol - through the existing Ethernet port, SW license is required,
· Communication via Profinet – with the special communication card,
· EtherCAT communication protocol developed by Beckhoff, with the special communication card,
· DeviceNet communication protocol – with the special communication card,
· CC-Link communication protocol - with the special communication card,
· Communication via User Socket Messaging - SW license is required.
If we compare this list with the list of protocols supported in D2000, at least two options can be used - Modbus TCP and Ethernet / IP protocols. The need of purchase of SW license for activation can be considered as a disadvantage (it costs about 500 – 1000 Euro per robot) – unless this protocol is already licensed in the specific application.
Third option is the communication via User Socket Messaging, which requires the license as well (price about 200 Euro).
In this case, it is the implementation of own communication protocol over TCP/IP in Karel programming language that is supported by Fanuc robots. There is necessary to program the robot and install this program to the each robot, what can be considered as the disadvantages.
The other option is usage of existing PLC, which already communicates with the robot, for the communication (e.g. Simatic S7 with which D2000 may communicate via Siemens SIMATIC S7 ISO on TCP protocol). This option depends on the conditions of the particular customer – if and what PLC co-operates with robot.
Which of the options did we try and finally recommend to the customer? You will find out it in the next blog.
Ing. Peter Humaj, www.ipesoft.com