Every new version of the IPESOFT D2000 brings support for new communication protocols and thus makes the platform more compatible. We already talked about the new communication features brought by the latest V21. In the first part of this blog post, I would like to introduce a very special feature that was implemented in the previous version V12.
OPC UA - universal protocol covering all communication requirements
Couple of years ago, we implemented the OPC UA communication protocol for industrial automation. First we implemented the OPC UA client and then (in the V12) we added the OPC UA server part. In general, OPC UA servers are software solutions that process data and enable conversion of the communication protocol used by the PLC into the OPC UA protocol. In this blog post, I would like to provide a basic overview of the protocol and explain why it has a significant future potential.
Why was OPC UA developed: A desire for a standard in industrial automation
Industrial automation has always been characterized by a great variety of communication devices, communication protocols and data types. This fact resulted in development of a broad range of communication protocols for industrial automation. Therefore, the integration of the data produced and the control of these devices has logically never been technically easy. For this reason, more than 80 communication protocols have been implemented in the D2000 over the last 25 years.
Of course, each of them has its specifics, requirements, strengths and weaknesses. Appropriately combining and setting up communication with these devices often required technically sighted employees and time. The growing amount of equipment and data produced in the factories has increased the demand for a universal protocol covering all communication requirements.
OPC vs. OPC UA: Evolution instead of revolution
Since the early 1990s a consortium of more than 6,000 manufacturers and customers of industrial automation has been trying to unify the protocols. They have formed the OPC Foundation (Object Linking and Embedding for Process Control). First, it was the OPC Classic communication standard, which was to be the coveted unifying standard.
Its shortcomings, especially the platform dependence on the Microsoft Windows architecture, performance and lack of security, prevented its mass use. Since 2006 there is a new standard in the world - OPC UA (Unified Architecture - a logical descendant of OPC Classic. Since the biggest drawbacks have been addressed, OPC UA is more of an evolution than a revolution. It supports different operating systems and provides better performance and security.
The protocol's potential is supported by the decisions of large automation solution suppliers, such as Bernecker&Rainer, Siemens or Rockwell Automation. They all decided to integrate this communication standard into their products. A communication via OPC UA can therefore, be for example used as an alternative in the latest series of Simatic S7 PLC devices.
The key features of this communication standard clearly include:
· openness (multiplatformity)
· security
· versatility
Let's take a closer look at the features.
How does OPC UA work: From sensor to ERP system
Unlike the OPC Classic, the OPC UA standard was designed from the beginning to be open and platform-independent. Both its specification and reference implementations are open-source and freely available to anyone.
Presently, there are even high-quality open-source implementations of this protocol. Although the standard itself is quite complex, it is not necessary to implement it in its entirety. A closed subset of functions, which the standard defines as a profile, will suffice.
Profiles are defined in hundreds of specifications. It is up to the supplier to decide how many features to support in their device or software. Both the client and the server inform each other at the beginning of the communication, which features they support. Therefore, it is possible for a chip with a memory of several tens of kB or an ERP system planning production for the entire company running on Linux, to communicate via OPC UA.
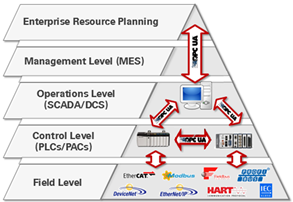
This feature, therefore, allows you to communicate through OPC UA at all levels of the company, such as:
· Machine to machine (M2M)
· Field & Control level (SCADA)
· Management Level (MES)
· Enterprise Level (ERP)
OPC UA security: PKI infrastructure at every step
Security is another integral feature of OPC UA communication. In essence, it is based on the "public key cryptography" (PKI) standard based on certificates, which is widespread today.
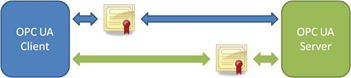
OPC UA security thus seeps through all levels of communication. It encompasses the transport layer with support for the latest cyphers and protocols such as TLSv1.3, digital signing, message encryption, application authentication and user login via client certificates.
Versatility of OPC UA
Data exchange via OPC UA is based on the object oriented concept of data processing. Objects represent real-world entities such as sensor, control unit, etc. and contain attributes with individual values. From the client's point of view, it is possible to read, write and monitor changes of attribute values. In addition to attributes, objects can also contain methods with parameters.
The methods implement the control aspect of the OPC UA protocol. The client application uses them to control the device and send instructions to it. In addition to methods, an object can publish the occurrence of a defined event that interests the client, e.g. alarm status of the device.
Objects can be organized in any tree structure, which consists of directories - special objects.
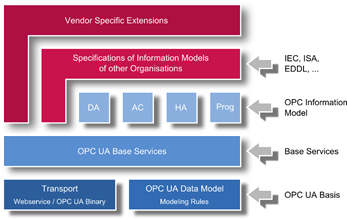
This universal data model is sufficient to represent data, events and operations in facilities of any industry. So that each manufacturer would not have to design their own information model, there are various standardized models for organizing this data for a given area of industry. We don't have to go far for illustration, because the OPC UA specification itself defines the basic general models. For example, that any measured analog quantity must have, in addition to the value itself, other attributes such as a timestamp or a quality flag, etc. Above this are models of other standards management organizations such as IEC 61804 (EDDL), ISA SP 103 (field device tool), ISA-S88, ISA-S95, etc.
Conclusion
From what has been written, it follows that OPC UA is still in the game for a universal protocol for years to come. Finally, this protocol was also declared the communication standard for "Industry 4.0". The next few years will show whether this will really happen. In any case, D2000 customers can take full advantage of this standard since 2019. The Part II of this blog post will describe how exactly does the OPC UA server work in the D2000 and how to use it to its full potential.
Ing. Marek Gregor, www.ipesoft.com